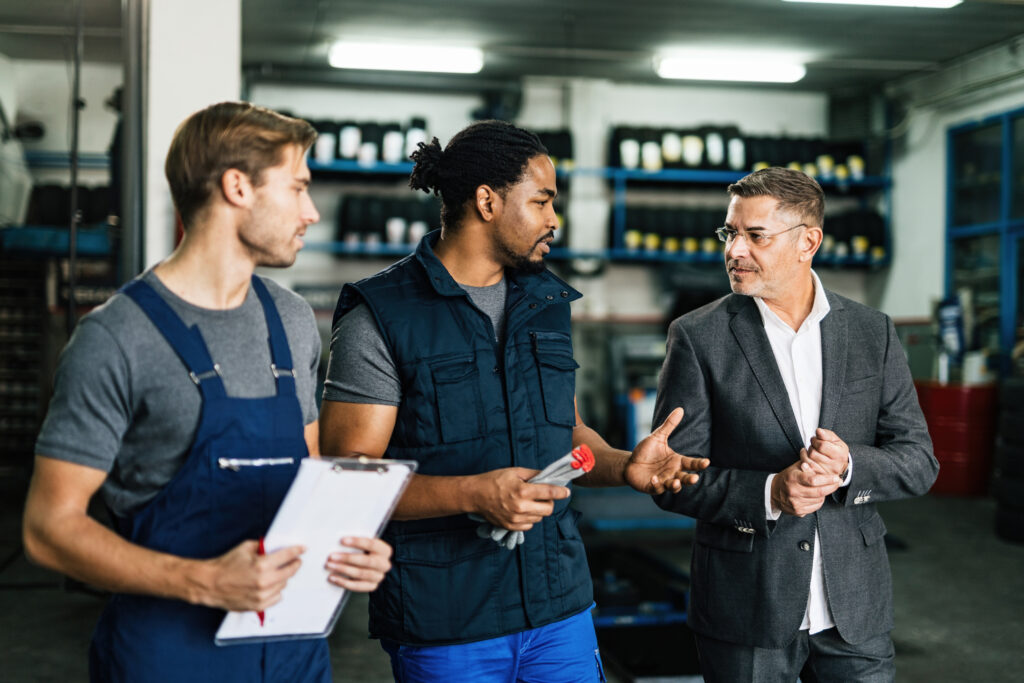
Consensus to Catalyst
We are advancing solutions key to decarbonizing the industrial sector by midcentury through policy development and advocacy, technology demonstration and adoption, and demand-side market development at state, regional, and federal levels.
The Industrial Innovation Initiative (I3) supports a consensus-driven and collaborative process that enables best practices to move from research to adoption and implementation.
A diverse coalition: The Industrial Innovation Initiative I3 brings together a diverse group of businesses, organizations, academics, and policymakers engaged in the research, technological advancement, and implementation of sound decarbonization strategies.
Working in collaboration: I3 is meeting the opportunity for US industry to become a global leader in technology investment and adoption, and seeking to ensure that the transition to net-zero is equitable and does not endanger the competitiveness of US industries and the communities they support.
Join more than 30 organizations working to achieve net zero by 2050. Request a member application.
Federal and State Policy Blueprint
I3 has developed a Federal Policy Blueprint in January 2024 outlining recommendations and strategies for advancing technology demonstrations, infrastructure deployment, market innovation, and other efforts to drive industrial decarbonization. See the initiative’s fact sheet, for these recommendations at a glance.
State Best Practices Guide (Click here for more info)
Policy recommendations on state actions to decarbonize the industrial sector — pairing high-level recommendations with real-world examples — to aid state decision makers and advocates seeking to cut emissions from essential industrial sectors such as cement, steel, and chemicals.
Policy Resources for the industrial sector
Key policy solutions needed to advance industrial decarbonization, include:
- Promote the development and deployment of clean industrial technologies.
- Provide financial incentives for decarbonization investments.
- Create a level playing field for clean energy technologies.
- Preserve a high-wage jobs base.
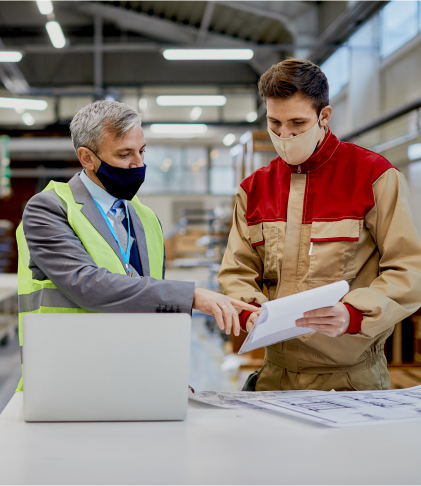
FAQs on Industrial Decarbonization
What is the industrial sector?
The industrial sector is responsible for many goods that structure and sustain everyday life, from buildings and bridges to detergents and fertilizers. Seven subsectors account for the majority of US industrial emissions: refining, steel, chemicals and fertilizer, cement, glass, forest products, and food and beverage processing.
Why is the industrial sector important to decarbonization?
Globally, the industrial sector is responsible for between 25% to 35% of greenhouse gas emissions, depending on whether electricity use is accounted for. The US industrial sector contributes about 25% of total domestic emissions, making it the third largest emitter, behind transportation and electric power. Decarbonizing the industrial sector will also be critical to meeting the US commitment of net zero by 2050.
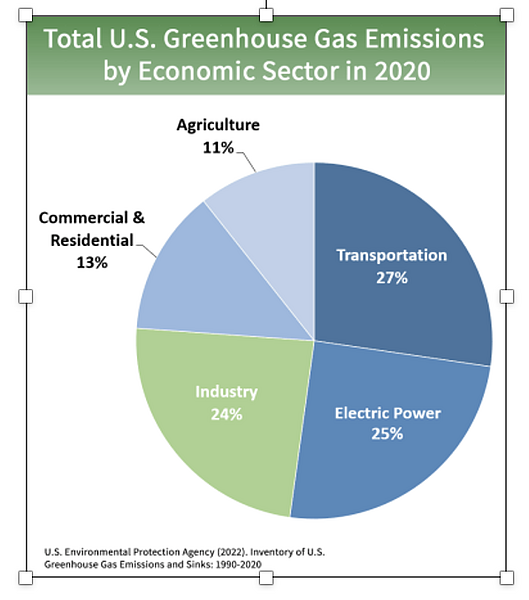
What industrial subsectors contribute most to industrial emissions?
Cement and concrete production, food products, iron and steel, bulk chemicals, and refining are the five industries that make up more than 50 percent of US industrial emissions. This is largely due to the large quantities of these goods being produced and the higher emissions intensity of their production.
What are the different types of industrial emissions?
Indirect emissions are emissions that are a consequence of the activities of the industrial company, but occur at sources owned or controlled by another entity — for example, energy that is produced offsite. Indirect emissions make up about 30% of the industrial footprint. Direct emissions make up the remaining 70% of industrial emissions. They come from sources that are owned or controlled by the industrial company.
These emissions occur at the facility and are grouped into two categories:
- The first category is fuel combustion emissions, which generate high-temperature heat or energy. Decarbonization solutions for fuel combustion include electrifying low-temperature heat processes, increasing energy efficiency, and switching to low-carbon fuels, such as clean hydrogen, for high-temperature heat needs.
- The second category is process emissions, which come from the chemical transformation of the raw material inputs to create an industrial product. For example, in the cement-making process, calcium carbonate (CaCO3) is heated in a cement kiln to form lime, and CO2 is emitted as a byproduct of that chemical reaction (learn more about cement production, here).
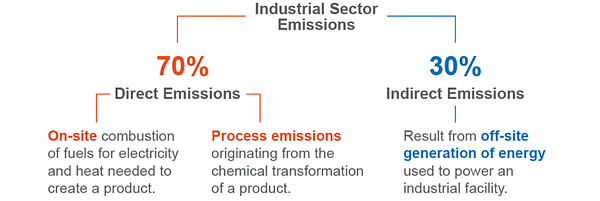
Why is the industrial sector often called “hard to decarbonize”?
There are a number of reasons the industrial sector has historically been labeled as “hard to decarbonize,”
- Decarbonization solutions will vary depending on the industry or region. The industrial facilities in each state vary, as do the emissions profiles and sources. The key to overcoming this challenge is to make the best possible use of existing resources and infrastructure where these facilities are sited.
- Historical lack of funding. Other sectors, such as the transportation or electric sectors have historically been the focus of decarbonization efforts and funding. Recently, there have been several efforts to increase the funding available for industrial decarbonization technology development and deployment. Historical lack of funding.
- Inherent process emissions and high-temperature heat needs. The variety of emissions in the industrial sector will require a portfolio of solutions. The high heat needed for some production pathways can not be easily electrified with our current technologies. Additionally, process emissions are inherent in the production of some products, such as steel and cement, and are unavoidable. However, these hurdles can be overcome with carbon management technologies and other novel technologies.
While there are challenges to decarbonizing this sector, we have the technology and solutions available to meet our goals.
Why does industrial decarbonization matter?
The industrial sector is an essential pillar of the US economy. This sector is responsible for providing the goods and services necessary for economic growth, supporting the demands of modern society. It is also responsible for innovation – developing new products, processes, and technologies. And perhaps most importantly, this sector creates jobs. Millions of Americans are directly employed in the five highest emitting sectors. To maintain and grow these jobs, which are most often high-quality and unionized, these sectors must decarbonize in collaboration with labor stakeholders. These industries also support a wide range of related businesses along the supply chain, from suppliers to distributors and service providers.
Industrial decarbonization is also a great opportunity to work with and improve the environment of local communities. Investments in decarbonizing industrial facilities provide an important opportunity to cut both greenhouse gas pollution and the associated co-pollutants that are harmful to public health and the environment.
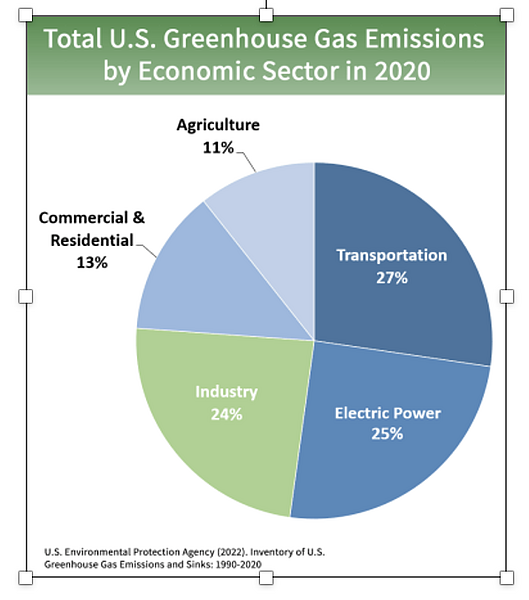
What are the key solutions for addressing industrial emissions?
Decarbonizing industry will require a diverse set of strategies in order to meaningfully reduce greenhouse gas emissions by midcentury given the variety and complexity of processes and emission sources across subsectors. The solutions cut across industrial sectors and include carbon management, low- and zero-carbon fuels, electrification, energy efficiency, and low-carbon procurement.
Federal incentives, such as the Bipartisan Infrastructure Law and the Inflation Reduction Act have laid the groundwork for the production of low-carbon industrial products. States can complement these programs by creating market demand and standards for lower-carbon industrial products through public procurement policies, such as Buy Clean.
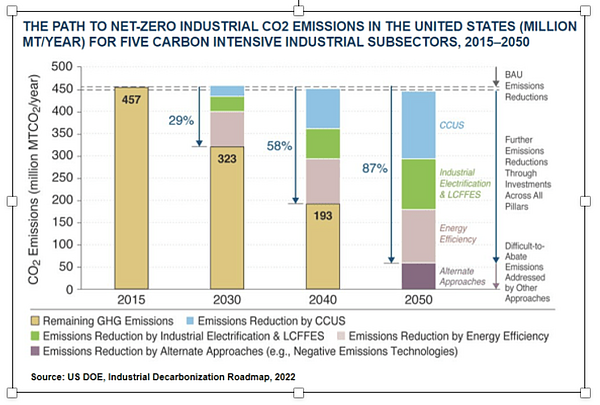
Within this decade, efficiency will play a leading role in emissions reductions for the industrial sector, with investments made today in electrification, low-carbon fuels, and carbon management investments that will scale up and take effect in the 2040s and 2050s. It is imperative that the deployment of efficiency solutions is accelerated for existing facilities through the support of incentives, standards, and technical assistance programs.
In advancing electrification and efficiency in existing facilities today, we can lay the foundation for the deployment and scaling of low- and zero-carbon molecular fuels (such as clean hydrogen), and carbon capture, reuse, and sequestration solutions, which will need to be operating at scale in the longer-term. Support for research and development exploring innovative manufacturing solutions will be needed across solution types and can take the form of pilot projects, tax credits, and other early technology investments. For policy recommendations on state actions to decarbonize the industrial sector, check out I3’s State Best Practices Guide which pairs high-level recommendations with real-world examples. For a deeper dive, see the US Climate Alliance’s State Policy Guidebook for Enabling Industrial Decarbonization.
What are the roles of electrification and energy efficiency?
Many steps in industrial processes that emit carbon dioxide can be electrified to reduce emissions without impacting the final product. Industrial energy customers have identified several processes that can be electrified, including industrial heating, compression, and even steam generation. Serving an energy need with electricity will continue to reduce emissions long after installation, as the electric utility sector continues to transition to low- or zero-carbon resources.
For example, if an industrial company chooses to serve an energy need with on-site fossil fuels, today, the emission profile associated with that resource will stay the same – or get worse – over its lifetime. However, by choosing to serve those energy needs with electricity, not only will the emissions shift from scope 1 to scope 2, but they will also decrease over time as the power sector transitions to renewables (solar and wind) and becomes cleaner.
Electrification is not without its challenges, many of which could be mitigated with state policies. These might include provisions that offset the cost of retrofit or replace existing equipment and ensure workforce development programs are in place to train contractors and installers of electric retrofits. Proposed policies and programs should also work with utilities to ensure reliability and resilience investments align with the increased use of the bulk electricity system. Additionally, incentives and fair regulatory structures for energy efficiency programs will aid in this transition.
A former Entergy CEO was famous for saying that as an electric utility, “we don’t want to sell waste.” All efforts to use electrical energy as efficiently as possible should be made because every kilowatt-hour of usage adds to a facility’s carbon footprint.
It is essential to pursue energy efficiency improvements in parallel with electrification to help offset expected increases in overall electricity demand. Efficiency measures also have additional co-benefits, including the reduction of overall operating expenses, which can, in turn, free up funds for other decarbonization solutions.
What is the role of hydrogen in industrial decarbonization?
Hydrogen is a clean energy solution because, unlike traditional fossil fuels, the only byproducts of hydrogen combustion are energy and water (2H2 + O2 –> H20 + energy). However, when it comes to the full lifecycle emissions profile, the production source of the hydrogen matters.
Most hydrogen is produced today using steam methane reforming (SMR), which uses fossil fuels and produces carbon emissions by stripping hydrogen atoms out of natural gas (primarily methane, CH4). This production process could be paired with carbon capture technologies to reduce emissions. Some see this pairing as a near-term solution for decarbonizing existing processes.
An alternative method is to produce hydrogen from electrolysis using zero-carbon energy. This pathway avoids the use of fossil fuels. Electrolysis is a process that runs an electrical current through water, splitting the molecule and releasing hydrogen and oxygen. If that electricity is from zero-carbon sources such as renewables or nuclear, the carbon footprint of that hydrogen is virtually zero.
Industrial facilities such as refineries and petrochemical plants require a lot of high-temperature heat, typically in the form of steam. The difficulty in decarbonizing this portion of industrial processes is the need to provide high-temperature “clean heat”. Lower-temperature steam needs will likely be met in the near future by electric boilers; however, larger and higher-pressure steam loads require a different solution – and clean hydrogen is one of the low-carbon fuel options that may be able to serve this need. Additionally, most of the hydrogen infrastructure that exists today, including pipelines and storage, are located in and amongst the facilities that need clean steam or that already use hydrogen as a feedstock (learn more about hydrogen here).
What does the carbon management process look like, start to finish?
Carbon management generally refers to carbon capture, removal, utilization, and sequestration. The first step in the process is capturing the carbon dioxide (CO2) from the flue gas of an emissions source, like a cement, steel, or iron production facility. This is referred to as point source capture. Once captured, CO2 is purified as necessary and compressed, then transported to a location where it can be permanently stored or reused. In some cases, the captured carbon can also be utilized onsite and doesn’t need to be transported. The most common and efficient form of transportation is by way of pipeline. The US has about 5,000 miles of existing CO2 pipelines, with over 50 years of operating experience.
Once transported, CO2 can be injected deep underground into geologic formations – the same formations that have locked away oil and gas and CO2 for millions of years, of which the United States has in abundance. The geologic sequestration of CO2 is not new; in fact, it has been in use for decades and industry has the tools to sequester CO2 safely and permanently. Regulations in the United States governing saline CO2 geologic sequestration are stringent and promote proper site selection, management, and site closure (learn more about carbon capture here).
The sequestration of carbon dioxide in geologic formations is governed by the Environmental Protection Agency’s Underground Injection Control (UIC) Class VI regulations, which are designed to protect underground sources of drinking water. They require an operator to undertake extensive site characterization, develop a comprehensive monitoring regime, adhere to specific well construction and injection standards, prepare emergency response plans, and hold financial assurance mechanisms. A recent study commissioned by the UK government showed CO2 retention rates in both depleted oil and gas fields and saline formations to be over 99 percent.
Another option, CO2 utilization, takes captured CO2 from either a point source or CO2 that has been captured directly from the air through a process called direct air capture and utilizes the CO2 as an input to create a product or service with a potential market value. There
are a range of potential applications and utilization is a complement to CO2 sequestration, with a varying range of permanent storage of CO2 depending on the lifetime of the product in which the CO2 is used.
CO2 is used in carbonated beverages, generated in ammonia production, and used on-site to manufacture urea (a nitrogen-based fertilizer), or used for enhanced oil recovery, but there is a wide range of potential applications. CO2 can be combined with hydrogen to create an ultra-low carbon-intensive fuel that can be used to help decarbonize sectors like shipping or aviation, with atmospheric CO2 combined with green hydrogen providing the biggest climate benefit.
CO2 can also be used in the production of concrete, becoming permanently stored in the concrete and if combined with atmospheric CO2, significantly decreases the carbon intensity of that concrete. It can also be incorporated into other building materials; a wide range of carbon-containing substances like plastics, solvents, and synthetic rubber; or a host of intermediate chemicals like ethylene or methanol. CO2 can also be used as a working fluid that replaces water in power generation — Net Power is an example of this use case. Carbon capture is widely recognized as a critical climate tool by the IEA, IPCC, and other organizations, and it is particularly important for industry. It will be nearly impossible to decarbonize heavy industries, such as cement, without relying on Carbon Capture, Usage and Storage (CCUS).In the IEA Clean Technology Scenario, which sets out a pathway consistent with the Paris Agreement climate ambition, CCUS contributes almost one-fifth of the emissions reductions needed across the industry sector.
Stay up to date!
i3 Monthly Newsletter — for news, strategies, and insights on industrial decarbonization.