In February 2023, the Industrial Innovation Initiative (I3) hosted an introductory webinar on industrial decarbonization for states, given the critical role they will play in reducing US industrial emissions. Supported by recent federal funding, namely from the Bipartisan Infrastructure Law and the Inflation Reduction Act, states are positioned to create a regulatory and policy landscape that spurs local implementation of this unprecedented funding and drives private investment.
Industrial decarbonization is a multifaceted challenge that will require a whole suite of policy solutions at the state level. It is also important to remember that states and facilities each have unique needs when decarbonizing. While there is no one-size-fits-all solution, a few key policies cut across industrial sectors and can be mixed and matched to greatly reduce a state’s industrial emissions.
View the webinar
I3 participants, Suzanne Caflish (BlueGreen Alliance), Angela Seligman (Clean Air Task Force), Kareem Hammoud (US Climate Alliance), William Swetra (Oxy Low Carbon Ventures), Jacqueline Clark (Holcim US), and Rick Johnson (Entergy), shared their expertise and experience with attendees and sought to answer the questions states and state advocates most often ask when first beginning work on industrial decarbonization.
What is the industrial sector?
The industrial sector generally refers to the material economy; it can be understood as the physical goods we mine, manufacture, consume, or use in construction. Globally, the industrial sector is responsible for between a quarter to a third of greenhouse gas emissions. The US industrial sector contributes about a quarter of total domestic emissions, making it the third largest emitter, behind transportation and electric power.
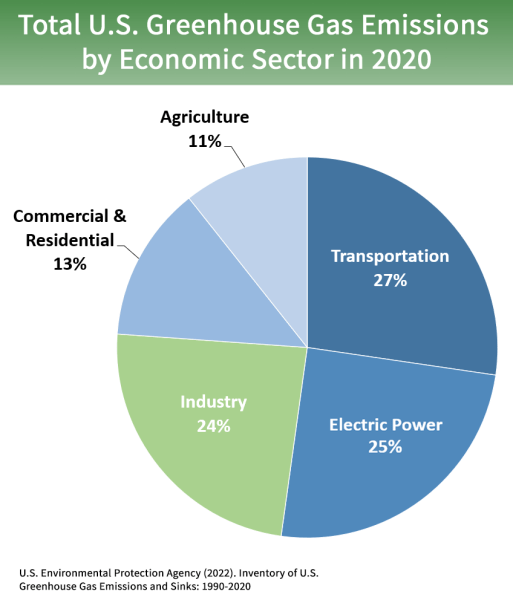
Even though “industry” is a large umbrella term, there is a short list of high-emitting industrial sub-sectors that make up the majority of emissions. Cement and lime, food products, iron and steel, bulk chemicals, and refining are the 5 industries that make up more than 50 percent of US industrial emissions. This is largely due to the large quantities of these goods being produced.
To provide a global example: the world makes 2 billion tons of steel per year. That breaks down to 1,000 pounds per person per year for everyone on earth. Steel goes into a variety of infrastructure and construction projects, like suspension bridges, runways, etc. That number is smaller when focusing on just the US, but still considerable (80 million metric tons).
Why is this sector often called, “hard to decarbonize”?
Despite having many solutions to significantly reduce emissions in the industrial sector today, it is still often referred to as being “hard to decarbonize.” The challenge with decarbonizing this sector is similar to the challenges facing any sector with significant emissions. The decarbonization solutions that will works best in a given state or region is closely tied to its infrastructure, geography, and climate, among other factors. The industrial facilities in each state vary, as do the emissions profiles and sources. The key to overcoming this challenge is to make the best possible use of the existing resources and infrastructure where these facilities are sited, and to support the technologies and markets necessary to rapidly and equitably bring these solutions to scale.
There are many energy inputs in the industrial sector, further complicating potential decarbonization options. Indirect emissions make up about a quarter of the industrial footprint and are the product of off-site energy production. These emissions will decrease as the grid this energy is pulled from decarbonizes.
Direct emissions make up the remaining 75 percent of industrial emissions and are grouped into two categories. The first category is fuel combustion emissions which generate high-temperature heat or energy. Decarbonization solutions for fuel combustion include electrifying low-temperature heat processes, increasing energy efficiency, and switching to low-carbon fuels, such as clean hydrogen, for high-temperature heat needs.
The second category is process emissions which come from the chemical transformation of the raw material inputs to create an industrial product. For example, in the cement-making process, calcium carbonate (CaCO3) is heated in a cement kiln to form lime, and CO2 is emitted as a byproduct of that chemical reaction (learn more about cement production, here). Cutting process emissions will require advancements in material efficiency, low-carbon feedstocks, and widespread use of carbon capture at industrial facilities.
Why does industrial decarbonization matter?
The industrial sector is an essential pillar of the US economy. This sector is responsible for providing the goods and services necessary for economic growth, supporting the demands of modern society. It is also responsible for innovation – developing new products, processes, and technologies. And perhaps most importantly, this sector creates jobs. Millions of Americans are directly employed in those same 5 most heavily emitting sectors. To maintain and grow these jobs, which are most often high-quality, and unionized, these sectors must decarbonize in collaboration with labor stakeholders. These industries also support a wide range of related businesses along the supply chain, from suppliers to distributors and service providers.
Industrial decarbonization is also a great opportunity to work with and improve the environment of local communities. Many industrial hubs are located alongside lower-income and underserved communities that are not in attainment with Clean Air Act standards. Investments in decarbonizing industrial facilities provides an important opportunity to cut both greenhouse gas pollution and the associated co-pollutants that are harmful to public health and the environment. States have the potential to show leadership in this rapidly evolving field in a way that takes an all-of-the above approach to pollution reduction to benefit local communities including reductions in carbon pollution, co-pollutants, and noise, light, and odor pollution.
What are the key policy solutions for addressing industrial emissions?
Just as the emissions sources and types vary state-by-state, so will the policy solutions. Near-term solutions should make use of the full potential of recent federal funding. Through intentional federal engagement, stakeholder outreach, and complementary state policies, the full amount of federal funding can be realized in local industrial projects.
Federal incentives have laid the groundwork for the production of low-carbon industrial products. States can complement these programs by creating market demand and standards for lower-carbon industrial products through public procurement policies, such as Buy Clean.

Within this decade, efficiency will play a leading role in emissions reductions for the industrial sector; with investments made today in electrification, low-carbon fuels, and carbon management investments that will scale up and take effect in the 2040s and 2050s. It is imperative that the deployment of efficiency solutions is accelerated for existing facilities through the support of state incentives, standards, and technical assistance programs.
In advancing electrification and efficiency in existing facilities today, we can lay the foundation for the deployment and scaling of low- and zero-carbon molecular fuels (such as clean hydrogen), and carbon capture, reuse, and storage solutions, which will need to be operating at scale in the longer-term. State support for research and development exploring innovative manufacturing solutions will be needed across solution types and can take the form of pilot projects, tax credits, and other early technology investments.
For policy recommendations on state actions to decarbonize the industrial sector, check out I3’s State Best Practices Guide which pairs high-level recommendations with real-world examples. For a deeper dive, see the US Climate Alliances State Policy Guidebook for Enabling Industrial Decarbonization.
What is the role of electrification and energy efficiency?
Many steps in industrial processes that emit carbon can be electrified to reduce their emissions without impacting the final product. Industrial energy customers have identified numerous energy needs where electrification is feasible, including industrial heating, compression, and even steam generation. Serving an energy need with electricity will continue to reduce emissions long after installation, as the electric utility sector continues to transition to low- or zero-carbon resources.
For example, if an industrial company chooses to serve an energy need with on-site fossil fuels, today, the emission profile associated with that resource will stay the same – or get worse – over its lifetime. However, by choosing to serve those energy needs with electricity, not only will the emissions shift from scope 1 to scope 2, but they will also go down over time as the power sector transitions and becomes cleaner.
Electrification is not without its challenges – many of which could be mitigated with state policies that include provisions which offset the cost to retrofit or replace existing equipment, ensure workforce development programs are in place to train contractors and installers of electric retrofits, and work with utilities to ensure reliability and resilience investments align with the increased use of the bulk electricity system. Additionally, incentives and fair regulatory structures for energy efficiency programs will aid in this transition.
A former Entergy CEO was famous for saying that as an electric utility, “we don’t want to sell waste.” All efforts to use electrical energy as efficiently as possible should be made because every kilowatt-hour of usage goes into your carbon footprint.
It is essential to pursue energy efficiency improvements in parallel with electrification to help offset expected increases in overall electricity demand. Efficiency measures also have additional co-benefits, including the reduction of overall operating expenses, which can, in turn, free up funds for other decarbonization solutions.
Why is hydrogen posed as a clean fuel source for industrial decarbonization?
Hydrogen is a clean solution because, unlike traditional combustion fuels, the only byproducts of hydrogen combustion are energy and water (2H2 + O2 –> H20 + energy). However, when it comes to the full lifecycle emissions profile, the production source of the hydrogen matters. Most hydrogen is produced today using steam methane reforming (SMR) – which uses fossil fuels and produces carbon emissions – by stripping hydrogen atoms out of natural gas (primarily methane, CH4). This production process could be paired with carbon capture technologies to reduce emissions. Some see this pairing as a near-term solution for decarbonizing existing processes.
Another production pathway is hydrogen derived from electrolysis using zero-carbon energy. This pathway avoids the use of fossil fuels. Electrolysis is a process that runs an electrical current through water, splitting the molecule and releasing hydrogen and oxygen. If that electricity is from zero-carbon sources such as renewables or nuclear, the carbon footprint of that hydrogen is virtually zero.
Industrial facilities such as refineries and petrochemical plants require a lot of high temperature heat, typically in the form of steam. The difficulty in decarbonizing this portion of the industrial processes is the need to provide high temperature “clean heat”. Lower-temperature steam needs will likely be met in the near future by electric boilers; however, larger and higher-pressure steam loads require a different solution – and clean hydrogen is one of the low-carbon fuel options that may be able to serve this need.
Additionally, most of the hydrogen infrastructure that exists today, including pipelines and storage, are located in and amongst the facilities that need clean steam or that already use hydrogen as a feedstock (learn more about hydrogen, here).
What does the carbon management process look like, start to finish?
Carbon capture involves first capturing carbon dioxide (CO2) from the flue gas of an emissions source, like a cement, steel, or iron production facility. This is referred to as point source capture. Once captured, CO2 is cleaned up as necessary and compressed, then transported to a location where it can be permanently stored or reused. The most common and efficient form of transportation is by way of pipeline. The U.S. has 5,000 miles of existing CO2 pipelines, with over 50 years of safe and successful operating experience.
Once transported, CO2 can be injected deep underground into geologic formations – the same formations that have locked away oil and gas and CO2 for millions of years, of which the United States has in abundance. The geologic storage of CO2 is not new, in fact, it has been in use for decades and industry has the tools to store CO2 safely, and permanently. Regulations in the United States governing saline CO2 geologic storage are stringent and promote proper site selection, management, and site closure (learn more about carbon capture, here).
The storage of carbon in geologic formation is regulated by the Environmental Protection Agency’s UIC Class VI regulations which are designed to protect underground sources of drinking water. They require, among many other items, an operator to undertake extensive site characterization, development of a comprehensive monitoring regime, adherence to specific well construction and injection standards, emergency response plans, and hold financial assurance mechanisms. There is also extensive academic research and peer-reviewed literature to indicate that CO2 storage can be done safely, and CO2 will be retained underground. A recent study commissioned by the U.K. government showed CO2 retention rates in both depleted oil and gas fields and saline formations to be over 99 percent.
Turning to CO2 reuse, by definition, it’s taking captured CO2 from either a point source or CO2 that has been captured directly from the air through a process called direct air capture and utilizing the carbon as an input to create a product or service with a potential market value. There are a range of potential applications and is a great complement to CO2 storage.
Most already know that CO2 is used in carbonated beverages, generated in ammonia production and used on-site to manufacture urea, or for enhanced oil recovery, but there is a wide range of potential applications. CO2 can be combined with hydrogen to create an ultra-low carbon-intensive fuel that can be used to help decarbonize hard to abate sectors like shipping or aviation, with atmospheric CO2 combined with green hydrogen providing the biggest climate benefit.
CO2 can also be used in the production of concrete, becoming permanently stored in the concrete and if combined with atmospheric CO2, significantly decreases the carbon intensity of that concrete. It can also be used in other building materials, a wide range of carbon-containing substances like plastics, solvents, synthetic rubber, or create a host of intermediate chemicals like ethylene or methanol. CO2 can also be used as a working fluid that replaces water in power generation, Net Power is an example of this use case.
Carbon capture is widely cited as a critical climate tool, by the IEA, IPCC, and other bodies, and it is particularly important for industry. It will be nearly impossible to decarbonize heavy industries such as cement without relying on CCUS. In the IEA Clean Technology Scenario, which sets out a pathway consistent with the Paris Agreement climate ambition, CCUS contributes almost one-fifth of the emissions reductions needed across the industry sector.
Want to learn more about industrial decarbonization?
For policy recommendations on state actions to decarbonize the industrial sector, check out I3’s State Best Practices Guide which pairs high-level recommendations with real-world examples.
Keep up to date with I3 news by signing up for our monthly newsletter. For more information on I3 or to get involved, contact Gabrielle Habeeb at ghabeeb@gpisd.net.