Decarbonizing the industrial sector has long been challenging due to the number of different subsectors and the variety of emissions sources. This is the first post in a series that will break down the complexities of industrial emissions by walking through the top four industrial subsectors and how we can decarbonize them. First up, decarbonizing our concrete landscape.
From skyscrapers to scraped knees, concrete is foundational in our world. And it is the most used human-made resource in the world. However, the emissions packed into this built environment are less noticeable in our everyday lives. Cement, the key ingredient in concrete, makes up about 7 to 8 percent of carbon dioxide (CO2) emissions globally, and 1.3 percent of total US emissions.
Key takeaways:
- Cement is the key ingredient in concrete, and cement production is responsible for most of the emissions associated with concrete.
- The cement sector is the world’s third-largest CO2 emitter. Globally, cement production releases around 2.7 billion metric tons of CO2 a year as of 2021, and it is expected to increase. That is the equivalent to over half a billion gas-powered cars driven for one year.
- Decarbonization solutions, including carbon capture, fuel switching, energy efficiency, and material substitutions, can be applied throughout the cement and concrete production process.
- Many solutions depend on the specific circumstances of a facility, and a supportive policy landscape will be essential to the widespread deployment of decarbonization technologies.
Concrete is a mix of cement, different sizes of crushed rock and sand, air, and water. While cement only constitutes around 10 to 15 percent of concrete by mass, it accounts for nearly 80 percent of its CO2 emissions. These numbers help explain why, if the cement industry were a country, it would be the third-largest emitter of CO2 behind China and the United States.
Demand for cement and concrete is increasing. This is largely due to a growing global population and urbanization. This sector is also critical to the global economy and workforce. The cement sector contributes over 5 percent of global gross domestic product, or GDP, and nearly 8 percent of employment worldwide.
How Concrete is Made: Cement Production, Emissions, and Emissions Solutions
So, how does a single industry end up producing such a large share of global CO2 emissions?
Before diving into the where and how of CO2 emissions from cement, it’s important to take a step back to understand why industrial emissions present a particular challenge when it comes to meeting midcentury net-zero targets in the US and abroad.
In industrial production, CO2 is emitted into the atmosphere in two ways: at the facility or at the power plant supplying the facility with electricity. Emissions released at the facility are called “direct emissions” and can come from combustion or non-combustion sources. Most industrial sector emissions originate from fossil fuels that are combusted for heat. The second type of direct emissions come from chemical reactions that release CO2 as a byproduct called “process emissions.” Because these emissions result from the chemical transformation of the materials, they are inherent to the production process. Common examples of industrial products that emit more process emissions than combustion emissions include steel, chemicals, and cement. Industrial processes also require energy from off-site electricity generation. These emissions from the power plant are called “indirect emissions.”
The difference between direct and indirect emissions is important when considering the full scope of solutions required for industrial decarbonization. However, direct emissions will play the biggest role in understanding why the process of making cement is so carbon-intensive.
Figure 1. Breakdown of Emission Sources from Concrete Production
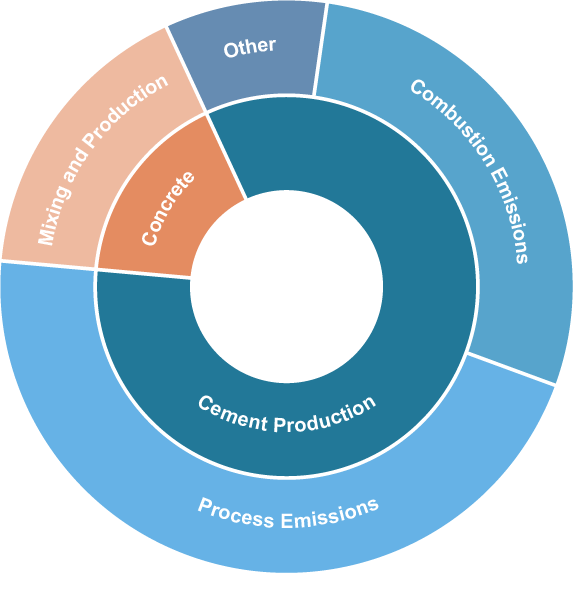
Cement production accounts for 80 percent of emissions in concrete. This is predominantly a mix of process (about half) and combustion (about a third) emissions from the kiln as explained in Step 2 of the production process outlined in the paragraphs below.
Graph based on data from the 2018 Energy Transitions Commission’s Mission Possible Cement Report.
Production Process
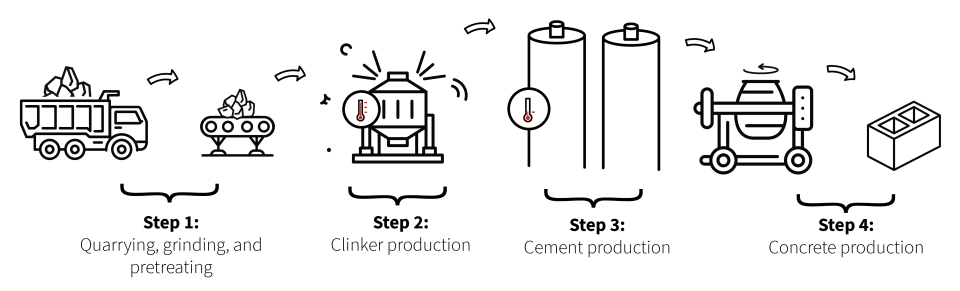
The concrete production process can be simplified to four major steps: quarrying, grinding, and pretreating, the production of clinker, the production of cement, and finally, the creation of the end product, concrete. This process outlined below includes possible decarbonization solutions intervening at each step.
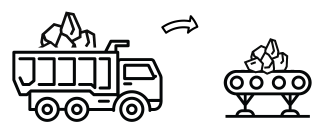
STEP 1: The first step in the cement process is the quarrying and grinding of raw materials, primarily limestone. The materials are ground into a fine powder. Depending on the facility, these materials undergo various pretreatments before entering the kiln for calcination.
ENERGY EFFICIENCY: Investment in upgraded equipment during the quarrying and grinding, or equipment for pretreatments, such as preheaters, and precalciners can improve the energy efficiency at the plant.
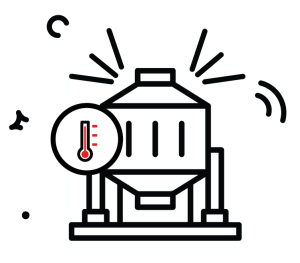
STEP 2: In a rotary kiln, the limestone mixture is heated to over 2,500 degrees Fahrenheit to produce clinker, the main, and most critical, ingredient in cement. This process is called calcination.
As the mixture is heated, it breaks down into calcium oxide (clinker) and CO2. The equation below shows how this transformation occurs. This step in the production process accounts for roughly 90 percent of the emissions associated with cement production, which is a mix of process and combustion emissions.
Calcination: CaCO3 (calcium carbonate from limestone) + heat (over 2,500 degrees) = CaO (calcium oxide – clinker) + CO2 (emissions)
CARBON CAPTURE TECHNOLOGIES: To address process emissions, carbon capture technologies play a critical role. Because these carbon emissions are released during the chemical transformation of the material, they are unavoidable. However, cement production facilities can be retrofitted with carbon capture equipment that captures the emissions from the precalciner or the kiln before they are released into the atmosphere. This captured CO2 is then transported to where it can be used beneficially in another product or process, such as concrete curing, or permanently stored underground.
FUEL SWITCHING: The high temperature needed in the kiln to produce clinker presents a challenge to reducing combustion emissions. Currently, many facilities use coal and natural gas to achieve high heat. Substituting these fossil fuels with lower-carbon feedstocks can help reduce these emissions. However, some alternatives have difficulty reaching those high temperatures—which is why biofuels, hydrogen, or waste feedstocks could be the most feasible options.
ENERGY EFFICIENCY: Improving the efficiency of kilns and clinker coolers can also help maximize energy productivity throughout the clinker production process.
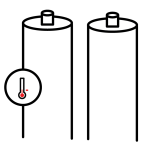
STEP 3: The clinker is then cooled before being blended with a small amount of gypsum, limestone, or other additives. The mixture is then ground to a powder to form cement. Cement produced in this manner is called Portland cement and is the most commonly used cement worldwide.
NOVEL & BLENDED CEMENTS: Novel, low-carbon alternatives to traditional Portland cement are being explored, such as alkali-activated cements. These cement types have different ingredients and can potentially lower process and combustion emissions during cement production. Another type of low-carbon cement, known as blended cement, is produced by lowering the clinker content with supplementary cementitious materials. However, many of these mixes face barriers to deployment, such as a lack of demand, prescriptive standards, and low public awareness. A supportive policy and regulatory landscape is needed for these novel cements to scale up.
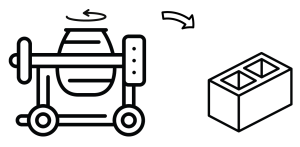
STEP 4: Last, the cement is mixed with water, aggregates, and sand to form the end product, concrete. Roughly 80 percent of the CO2 emissions from concrete come from the cement production process. The other 20 percent comes from the energy needed for activities across the value chain, including quarrying, transport, grinding, etc.
Concrete = Cement + water + aggregates + sand
MATERIAL SUBSTITUTION: Reducing the carbon intensity of concrete typically starts with reducing the cement content and replacing it with supplementary cementitious materials. Cement acts as the binding agent, or glue, in concrete. When the amount of cement is reduced, it needs to be replaced with another glue. This can include materials such as natural pozzolans or some industrial waste materials, including fly ash or steel slag. Pozzolans are a type of material that, when mixed in water, react to form a cementitious compound, similar to Portland cement. Alternative aggregates can also be substituted to reduce the carbon intensity of the material. This can include recycled concrete, agricultural waste, or synthetic aggregates.
Policy Landscape & Market Solutions
The applicability of each of these decarbonization solutions is often dependent on the local context of an industrial facility, such as the facility’s age, the availability of alternative fuels and materials, and the proximity of infrastructure for transport, use, or storage of captured CO2. Additionally, many of the solutions described have various levels of technological readiness and cost considerations, making a supportive policy landscape crucial for spurring deployment.
Procurement policies are one type of policy instrument that can create favorable market conditions for deployment. Procurement of low-embodied carbon materials requires disclosure, incentives, and standards to leverage the purchasing power of public agencies at the federal, state, or local level and, less frequently, by private building owners.
Several best practices can be considered when designing an effective procurement policy:
- Implementing effective procurement practices requires comparable, easily reported data on emissions intensity across products (i.e., disclosure). This is commonly achieved through environmental product declarations, or EPDs, which are sometimes compared to a nutrition label for construction materials.
- Complementary incentives can encourage early participation and broader implementation from industry through financial support for technological upgrades, technical assistance or bid incentives.
- Setting emissions limits and benchmarks for eligible products encourages domestic manufacturing and innovation while discouraging emissions outsourcing. To discourage emissions leakage, some countries are also considering a carbon border adjustment mechanism to tax imported cement and concrete based on their carbon intensity.
Effective procurement policies can leverage government purchasing power to play a significant role in supporting domestic manufacturers by creating a demand for green products. With last year’s Bipartisan Infrastructure Law only increasing demand for cement in domestic infrastructure projects, both state and federal agencies are poised to play an essential part in defining sustainable procurement policy informed by industry.
In December 2021, the Biden administration announced its Federal Sustainability Plan and Executive Order 14057, launching a Buy Clean Task Force to promote the use of low-carbon, made-in-America construction materials. In response, the General Services Administration issued its first “Buy Clean” standard for concrete, and the Department of Transportation released its first agency-wide “Buy Clean” policy to bolster more sustainable procurement practices across its programs. Additionally, in September 2022, the federal government announced that it will prioritize the purchase of concrete with lower levels of embodied greenhouse gas emissions.
Meanwhile, many states have passed or introduced legislation to promote the use of low-carbon concrete in public projects, including California, Colorado, New Jersey, and Oregon.
Procurement policies are only one side of the equation. To use novel and blended lower carbon, cement and concrete mixes in construction projects, less prescriptive, performance-based material standards must also be adopted and promoted for use of these mixes
As government officials design domestic decarbonization policies, it will also be key to consider trade policy and the global marketplace to avoid offshoring cement and concrete manufacturing and the leakage of associated emissions to less regulated countries. International cooperation can play an important role as well. Coalitions like the Industrial Deep Decarbonization Initiative, with the US as its newest member, can encourage the use of green public procurement and the adoption of harmonized and ambitious standards for low-emission cement.
Several emerging technologies will be required to achieve cement sector decarbonization on a 2050 timeline—but these vary widely in terms of cost, timeline for deployment, and maturity. For instance, while carbon capture technologies will be essential for the industry to reduce emissions in the long term, carbon capture has not yet reached a commercial scale of deployment. Likewise, novel cements and alternative materials will require further research and development to enable near-term use. For the cement sector to decarbonize, research, development, and demonstration for both near- and long-term solutions will be critical to achieving cost-effective and timely deployment.
By creating a favorable market and policy environment, these policies can retain and generate workforce opportunities and bolster the US manufacturing sector, ensuring decarbonization along each step of the value chain.