Steel is woven into every aspect of our lives. It is the backbone of iconic monuments and buildings as well as everyday objects like cars and cookware. We have used steel for nearly 4,000 years because of its durability and versatility. What starts as iron ore is refined, impurities are removed, and carbon is added until we are left with steel. Iron is a very common element in the earth’s crust, but pure iron is much harder to come by; it almost always exists with oxygen (in the form of iron ore), which needs to be removed to turn steel into the strong, easy to use material that we rely on.
Key Takeaways:
- While we rely on steel in many aspects of our lives, its production releases significant emissions. In 2021, the steel sector released over 62 million tonnes of CO2.
- There are two primary methods for steel production, integrated mills and minimills. Integrated mills use blast furnaces and basic oxygen furnaces to convert iron ore to steel. Minimills use recycled steel and electric arc furnaces. The majority of steel in the US is produced through this pathway.
- While the process of steel production is complex, it can be simplified into four main steps: mining and preparing the ingredients, creating iron, steelmaking, and lastly, casting and rolling.
- As with many industrial sectors, decarbonization solutions for steel production are often dependent on the individual facility. At a high level, fuel switching, carbon management, and efficiency in both the material use and operation of facilities will be key technologies across the sector.
This process of converting iron ore to steel, however, can create significant emissions. Globally, steel contributes to seven percent of total greenhouse gas (GHG) emissions. In 2021, the US steel sector released over 62 million tones of CO2 emissions That’s equivalent to roughly 14 million fossil-fuel cars on the road every year. There are 79 iron and steelmaking facilities in the US today, with most of this activity concentrated in the Upper Midwest and Great Lakes regions. These 79 facilities have the capacity to produce over 121 million tons of steel per year.
Figure 1. Map of US iron and steel production facilities
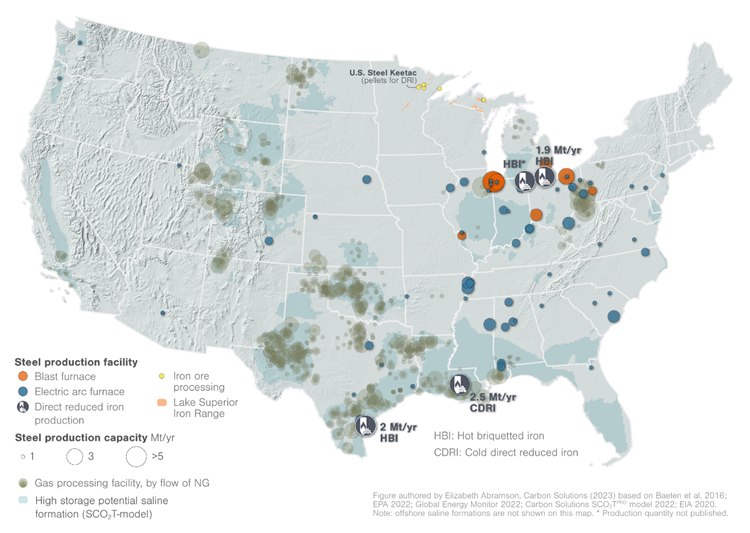
More information on types of emissions, and why the industrial sector broadly presents a particular challenge for decarbonization, can be found in the first blog in this series. This blog will focus on the direct emissions from the steel sector i.e., emissions from the steel plant, which can be divided into process and combustion emissions. Process emissions result from the chemical transformation of materials to create a final product, whereas combustion emissions result from burning the fuels needed to meet the high heat requirements to process raw materials into finished products. Direct emissions do not include emissions from sources outside the steel plant, such as off-site electricity production, known as indirect production.
How Steel is Made: Steel Production, Emissions, and Emissions Solutions
So how does a lump of iron turn into a stainless-steel frying pan? Like any good omelet, it starts with raw ingredients. For steel, the three main ingredients are iron ore, coal, and scrap steel (i.e., recycled steel).
There are two main production routes in US steelmaking: integrated mill production and minimill production. Integrated mills mainly use iron ore and coal as raw materials to produce steel. The integrated mill production route uses a blast furnace to remove oxygen and other elements from the iron ore resulting in nearly pure iron with trace amounts of carbon. It also uses a basic oxygen furnace to further fine-tune the properties of the steel. Using the blast furnace/basic oxide furnace route is known as primary steel production.
Alternatively, minimills principally use scrap steel as an input and an electric arc furnace to melt the scrap and create new steel products, this is also known as secondary steel production. Close to 70 percent of the steel produced in the US is done through the electric arc furnace route. Using recycled scrap inputs can reduce process emissions from steel production, while electric arc furnaces can use clean energy from the grid. The US already has a high steel recycling rate of upwards of 85 percent, but the availablity scrap steel is finite. With demand for steel only expected to increase with the transition to cleaner forms of energy, it will be critical to reduce emissions from steel production.
Production Process

At a high level, there are four main steps in the production process.
STEP 1: Material Preparation – First, iron ore and coal are mined. Once out of the ground the raw materials are brought to the stacker/reclaimer where they are sorted by grade, or quality. Then the iron ore is sent off to the sinter plant. Here, the iron has impurities removed and is mixed with other recycled materials to create sinter, which is a small cluster of iron ore. The coal goes to the coking plant where it is heated to 1250 C to remove any impurities. This results in coke, a porous substance that is nearly all carbon.
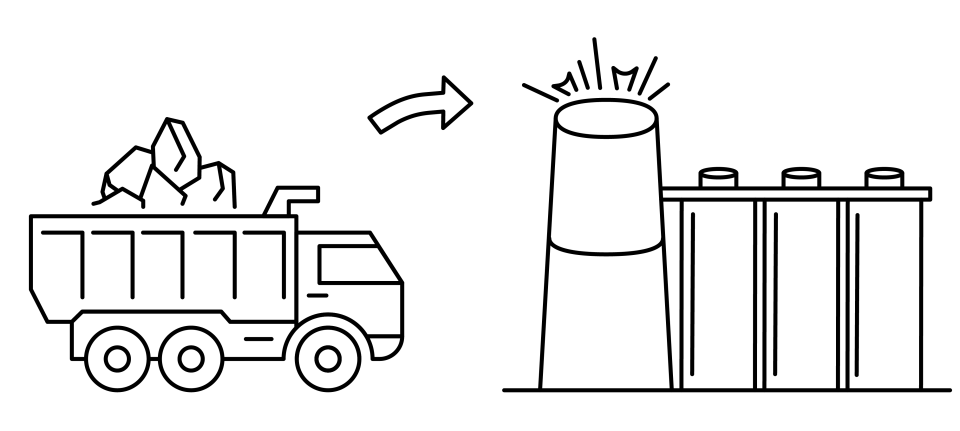
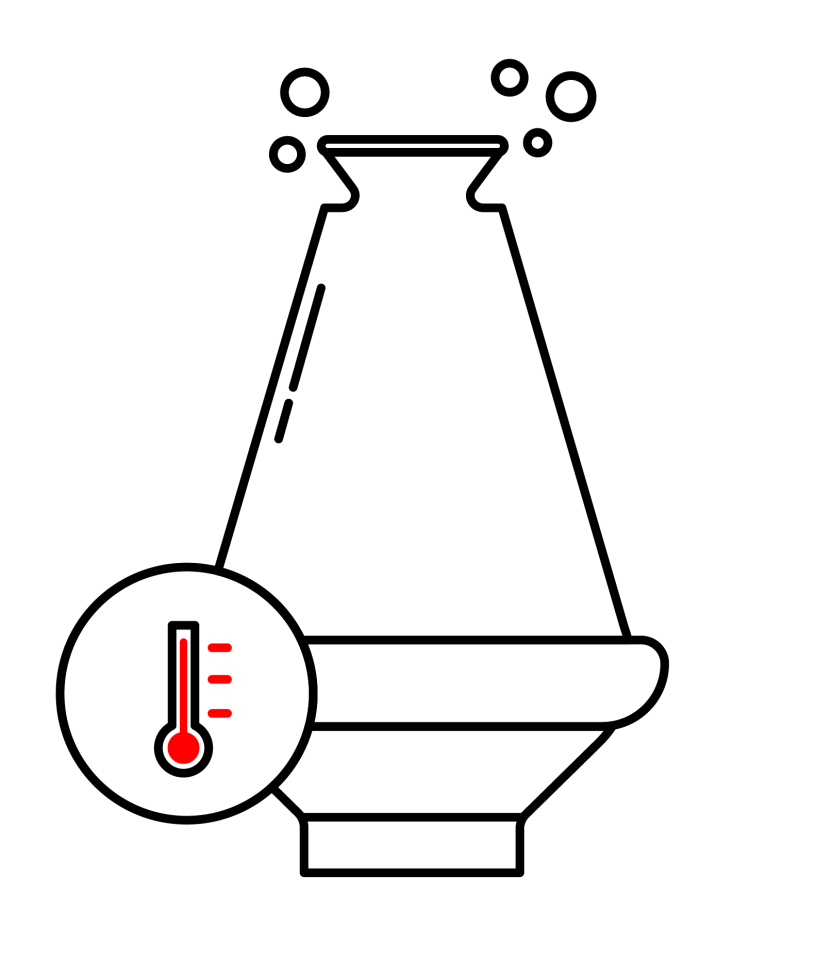
Step 2: Ironmaking – The iron then needs to have oxygen removed. This is called “reduction” and can happen in a few ways. Traditionally, this is done through the blast furnace/basic oxide furnace route: in a blast furnace hot air is blown into a mix of coke, sinter, and lime resulting in molten ’pig iron’, an intermediary material with 4 percent carbon. This process produces CO2 and slag as byproducts. Slag is a mixture of minerals that is removed during the purification process. It can also be used in other sectors, such as cement production. A simplified form of the equation for this chemical transformation of iron ore to iron and CO2 is below.
Equation: FeO (Iron + Oxygen, aka Iron Ore) + CO (Coke) + Heat -> Fe (Pure Iron) + CO2
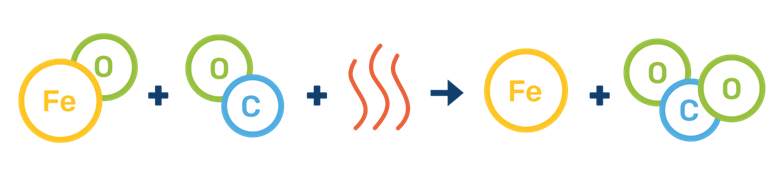
Alternatively, the iron ore could go to a direct reduced iron (DRI) furnace for reduction into ‘sponge iron’. These furnaces use a pelletized form of iron instead of sinter and are mixed with scrap steel. Typically, they use natural gas instead of coke for combustion. Technologies like DRI that use alternatives to coke, such as coal, natural gas, or biocoal can also achieve reductions in emissions. These technologies usually involve the suspension of iron ore in the DRI furnace, rather than relying on coke, to provide a solid, porous structure favorable for heating and reduction. Additional clean iron-making technologies that target the process emissions from iron reduction can include carbon capture on blast furnace production and DRI when using natural gas or alternative fuels.
Process emissions can also be eliminated by using alternative iron-ore reduction gases, such as hydrogen and electrolysis. Using clean hydrogen as an iron-ore reduction gas eliminates carbon emissions from the steelmaking process. Compared to blast furnaces, DRI has the potential to reduce greenhouse gas emissions from the steelmaking process by up to 99% when paired with carbon-free hydrogen. There are many initiatives and pilot programs aimed at developing this technology. Electrolysis can also be used to reduce iron ore by using electrodes and a liquid oxide electrolyte at high temperatures to separate iron from oxygen and other elements found in iron ore, thus eliminating the need for reduction by a blast furnace.
STEP 3: Steelmaking – The next step is using a furnace to blow oxygen into the molten iron. This reduces carbon content which is necessary to create a stronger material., and again there are a few different production options. In the blast furnace/basic oxide furnace process, the basic oxygen furnace blows oxygen into the molten iron to reduce the carbon content to 1 percent, which is ideal for the strength needed. The steel that is produced is then ready for casting, or depending on the grade, it is treated further before the next step. Another option is an electric arc furnace. These can convert steel scraps or sponge iron from the DRI process into liquid steel. They also produce slag as a byproduct.
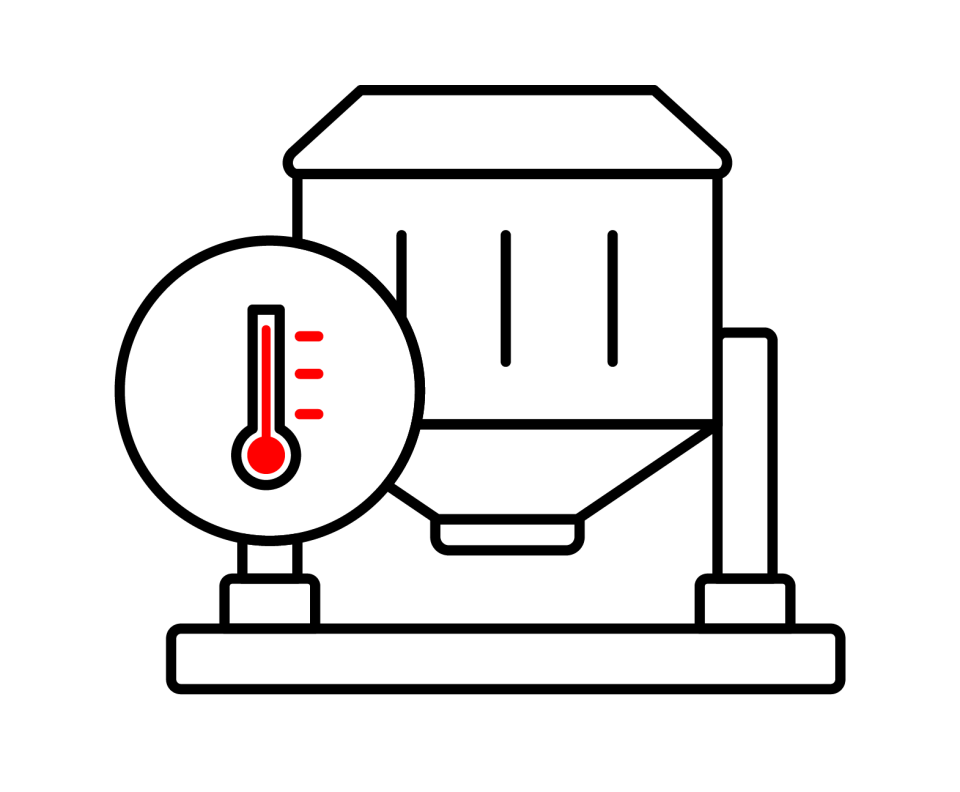
Figure 2: Amount of Steel Production in the US by Technology at Individual Facilities
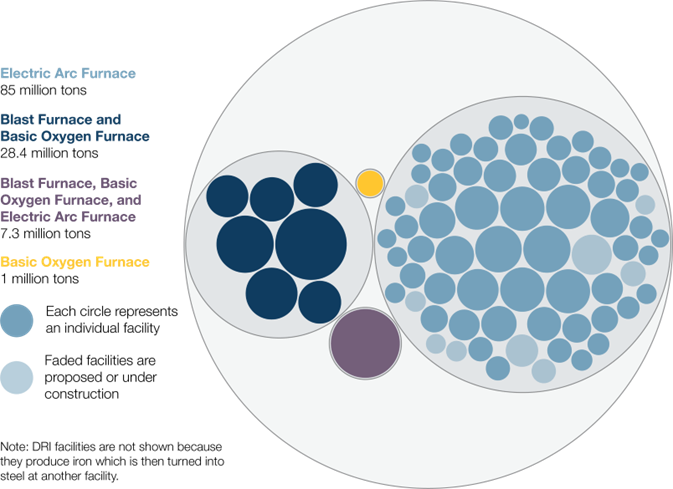
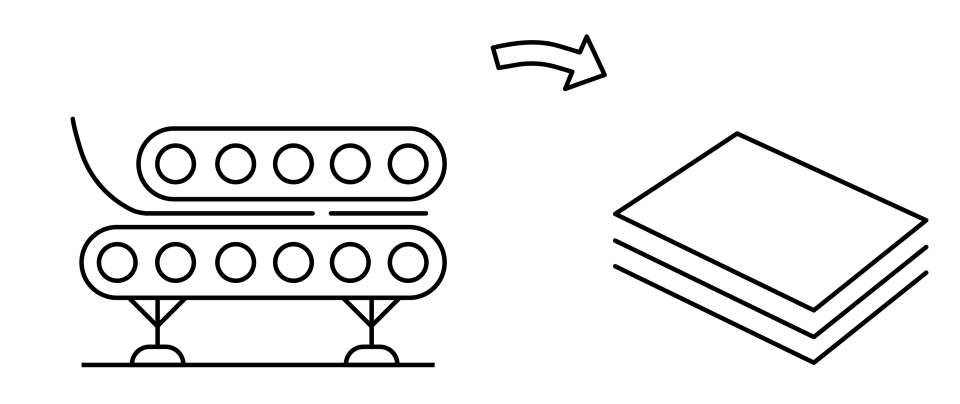
STEP 4: Casting and Rolling – Now that the iron has been reduced into steel, it is ready to be cast and rolled into useful shapes. The liquid steel from the furnace is brought to the continuous casting machine where it is poured into a mold and becomes a slab of steel. This slab then goes to the hot roller where it is heated to 1200 C and rolled out until it reaches the desired thickness. Sometimes, the slab then moves to the cold roller, which allows for more precise dimensions. These rolling processes produce steel in a variety of shapes and sizes depending on the end products. Lastly, finishing treatments such as annealing, galvanizing, or organic coating are applied as needed to create the desired qualities of the steel.
Policy Landscape & Market Solutions
As with any industrial sector, steel will require its own comprehensive set of technological tools to decarbonize in the coming decades:
- Pilot demonstrations for zero-emission technologies and lower-carbon steel production methods for commercial deployment post-2030, such as hydrogen DRI for Electric Arc Furnaces, Carbon Capture on Blast Furnaces, and Molten Oxide Electrolysis.
- Fuel and feedstock switching from fossil fuel sources to hydrogen as an alternative iron-reducing agent for DRI, and electrification to support alternative methods of production such as molten-oxide electrolysis.
- Buildout of transportation and storage infrastructure for captured CO2 and hydrogen.
- Materials and operating efficiency including policies and practices to optimize material use, maximize scrap steel recycling and increase circularity, and measures such as waste heat optimization and monitoring and automation for operating efficiency.
As cleaner steel enters the marketplace, supportive demand-side policies can help provide the certainty required for private investment to begin. Pairing public low-carbon procurement policies or corporate buyers’ clubs with standards such as Responsible Steel can help ease uncertainties around risk and create a market for DRI technology and lower-carbon steel for construction projects. Consideration of international trade implications for domestic industry will be important as well, given that carbon border adjustments are being considered in domestic legislation and continue to develop in the European Union.
Supporting the scale-up of clean steel supply will require adequate demand and integrated efforts across the public and private sectors. The first blog in this series describes these policies, applicable across construction materials, in more detail. For a greater foundation of the decarbonization challenges and policy solutions available for the steel sector, watch the Industrial Innovation Initiative’s Steel Sector Overview, which provides more information on the practical experiences of companies working to advance decarbonization across the value chain.